Closed-cell spray foam insulation requires minimal maintenance once properly installed, but periodic inspections and basic upkeep ensure optimal performance and longevity. Unlike traditional insulation materials that may settle, compress, or deteriorate over time, closed-cell foam maintains its structural integrity and insulating properties for decades with proper care.
The key maintenance activities include annual visual inspections for cracks or damage, maintaining proper ventilation to prevent moisture buildup, and addressing any structural issues promptly. Raleigh Excel Spray Foam Insulation has observed that properly maintained closed-cell installations can perform effectively for 30+ years without significant degradation.
This comprehensive guide examines the specific maintenance requirements, warning signs to monitor, and best practices for preserving your closed-cell spray foam investment based on extensive field experience and industry data.
Understanding Closed-Cell Spray Foam Durability
Closed-cell spray foam creates a rigid, impermeable barrier that resists moisture, air infiltration, and structural movement. The cellular structure consists of tiny, sealed bubbles that provide superior strength compared to open-cell alternatives. This inherent durability translates to reduced maintenance requirements compared to traditional insulation materials.
The foam’s chemical composition undergoes complete curing within 24-48 hours, creating a stable polymer structure that resists degradation from temperature fluctuations, humidity, and normal building movement. Industry studies indicate that properly installed closed-cell foam maintains 95% of its original R-value after 20 years of service.
Essential Maintenance Requirements
Annual Visual Inspections
Conduct thorough visual examinations of exposed spray foam surfaces each year, focusing on areas where mechanical damage or settling might occur. Check for hairline cracks, discoloration, or surface irregularities that could indicate underlying issues.
Bonus Tip: Schedule inspections during extreme weather changes when expansion and contraction stresses are most apparent. Spring and fall transitions reveal potential problem areas before they become significant issues.
Moisture Management
Monitor humidity levels in conditioned spaces to prevent condensation that could affect foam performance. Maintain indoor humidity between 30-50% to optimize foam longevity and prevent moisture-related complications.
Examine areas around plumbing penetrations, electrical outlets, and mechanical systems where water intrusion might compromise foam integrity. Address any moisture sources immediately to prevent structural damage.
Structural Monitoring
Assess building movement and settling that might stress spray foam installations. Pay particular attention to expansion joints, foundation interfaces, and areas where different building materials meet.
Maintenance Task | Frequency | Critical Areas | Warning Signs |
---|---|---|---|
Visual Inspection | Annually | Penetrations, joints, exposed surfaces | Cracks, discoloration, separation |
Moisture Check | Quarterly | Basements, crawl spaces, attics | Condensation, humidity >60% |
Structural Review | Bi-annually | Foundation interfaces, expansion joints | Movement, gaps, compression |
Professional Assessment | Every 5 years | Entire installation | Performance degradation, efficiency loss |
Climate-Specific Maintenance Considerations
North Carolina’s humid subtropical climate creates unique challenges for spray foam maintenance. High summer humidity combined with temperature fluctuations requires attention to vapor management and thermal cycling effects.
Monitor foam performance during extreme weather events, particularly ice storms and heavy rainfall that can stress building envelopes. The region’s occasional freeze-thaw cycles may cause minor expansion and contraction that requires periodic assessment.
According to the North Carolina Building Code Council, properly maintained spray foam insulation in the state’s climate zone maintains effectiveness for 25-30 years with minimal intervention.
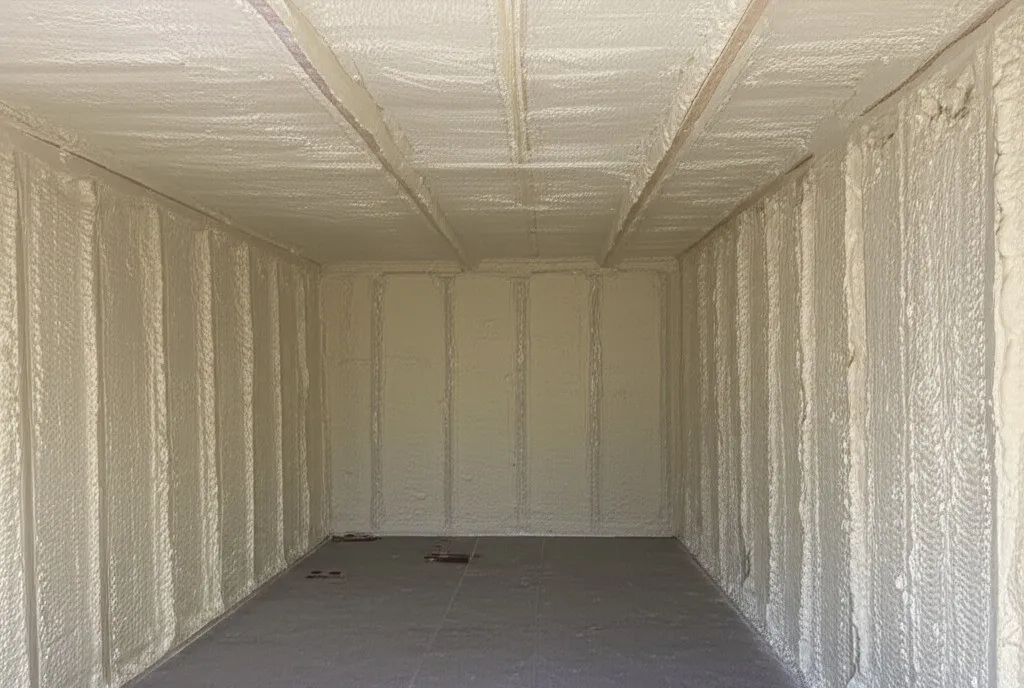
Things to Consider Before Making Maintenance Decisions
Evaluate your building’s age and construction type when developing maintenance schedules. Newer structures with engineered systems may require different approaches than older buildings with traditional construction methods.
Consider the accessibility of spray foam installations when planning maintenance activities. Areas behind finished walls or in confined spaces may require professional assessment rather than DIY inspection.
Budget for periodic professional evaluations, especially in commercial applications where energy efficiency directly impacts operational costs. The Department of Energy reports that proactive maintenance can prevent 15-20% energy efficiency losses over time.
Assess your comfort level with maintenance tasks versus professional services. While basic inspections are straightforward, identifying subtle performance issues often requires specialized knowledge and equipment.
Professional Spray Foam Services
Raleigh Excel Spray Foam Insulation provides comprehensive maintenance and assessment services to ensure optimal performance:
- Closed-Cell Spray Foam Insulation: Complete installation with detailed maintenance guidance and long-term performance monitoring
- Commercial Spray Foam Insulation: Specialized maintenance programs for commercial properties with scheduled inspections and efficiency assessments
- Residential Spray Foam Insulation: Homeowner-focused maintenance education and periodic professional evaluations
- Roof Insulation: Comprehensive roof foam maintenance including moisture management and structural assessment
Maintenance Best Practices and Long-Term Care
Document all maintenance activities including dates, observations, and any corrective actions taken. This record helps identify patterns and supports warranty claims if issues develop.
Bonus Tip: Create a simple maintenance log with photos of key areas during initial inspections. This baseline documentation makes it easier to identify changes during future evaluations.
Maintain consistent environmental conditions in conditioned spaces to minimize thermal stress on spray foam installations. Rapid temperature changes can cause expansion and contraction that may lead to cracking or separation over time.
Bonus Tip: Install temperature and humidity monitoring systems in critical areas like basements and attics. These provide continuous data that helps identify potential issues before they become visible problems.
Protecting Your Investment
Proper maintenance preserves the significant energy savings and comfort benefits that closed-cell spray foam provides. The Building Performance Institute estimates that well-maintained spray foam installations can reduce energy costs by 30-50% compared to traditional insulation materials.
Understanding maintenance requirements helps homeowners and building managers make informed decisions about their insulation investments. Regular attention to basic maintenance tasks prevents costly repairs and ensures optimal performance throughout the foam’s service life.
Getting Professional Support
For comprehensive maintenance evaluation and expert guidance on your spray foam insulation system, contact Raleigh Excel Spray Foam Insulation at (919) 301-9435 or [email protected]. Professional assessment ensures your installation continues delivering maximum energy efficiency and comfort benefits for years to come.
Common Maintenance Questions
How do I identify spray foam degradation?
Look for visible cracks, color changes from white/cream to yellow or brown, soft spots when pressed, or areas where foam appears to be pulling away from surfaces. These signs indicate potential moisture damage or chemical breakdown.
What causes spray foam to fail prematurely?
Common causes include improper installation ratios, inadequate surface preparation, exposure to chemicals or solvents, excessive moisture, and extreme temperature cycling beyond design limits.
Can I repair damaged spray foam myself?
Minor surface repairs may be possible with appropriate products, but structural damage or significant areas require professional assessment and repair to maintain insulation integrity and building performance.
How often should professionals inspect my spray foam?
Schedule professional evaluations every 5 years for residential applications and every 2-3 years for commercial properties. Older buildings or those with known moisture issues may require more frequent assessments.
What tools do I need for basic maintenance?
Essential tools include a high-quality flashlight or headlamp, digital hygrometer for moisture measurement, basic hand tools for accessing inspection areas, and a camera for documenting any issues discovered during inspections.